Special structures for special loads
From A to B
and in between
Docking of up to 3,000 kg, particularly sensitive components, complex tools, drawn-in chains, empty warp beams - these are just a few special cases for which there can be no standard in intralogistics. And there must not be for the safety of people and materials.
Transport trolleys from Genkinger are always custom-built solutions, specified for the respective loads and designed for a wide variety of situations and tasks on site. For example, transport trolleys from Genkinger are used in weaving and knitting mills not only for transport, but also for storage, intermediate storage and as collection trolleys (order picking).
- Gentle transport of material
- Orderly (intermediate) storage
- Variable width
- Electric or manual
More mobile assembly:
Pivot point
for assemblies
If the further assembly of assemblies or vehicles and machines is to be kept as flexible as possible, new transport solutions are needed within manufacturing as an alternative to rails and belts. As the size, weight and bulkiness of assemblies increase, so do the demands on transport. The pivotal point is also the device for safe pickup as well as precise feeding of the assemblies.
Genkinger designs industrial trucks with a high level of vertical integration. This enables specific configuration, even for different transport tasks with a single vehicle.
- Simple and safe operation via radio remote control and safety interrogations
- Flexible (rotary) fixtures with different adapters or vacuum grippers
- Optimized for small batch assembly, vehicle manufacturing and mechanical engineering
Everything under control in the weaving & knitting mill
Sovereign security
in any situation
When transporting docks and merchandise trees, it is important to solve these three situations in particular with confidence:
- The removal of the dock from the dock winder or the removal of the fabric beam from the weaving machine
- The safe transport, also over longer distances, on small and also uneven surfaces
- The safe unwinding of the dock or fabric beam down to the floor, to intermediate heights or up to the high rack
Genkinger develops customized transport solutions for docks and goods trees with different weights, lengths and diameters, always also adapted to the conditions and requirements on site.
- Docks & fabric trees up to 3,000 kg
- Different lengths and diameters
- Also double-sided overrolling and unrolling from the floor to the high rack
Project
EE-GM 25...30: Transport trolley
- Load capacity Q 2.500 kg
- Machine width 600 mm - infinite
Project
KEGU 50: Transport trolley
- Load capacity Q 5.000 kg
- Machine width 600 mm - infinite
Describe your case.
We will be glad to advise you.
Describe your case.
We will be glad to advise you.
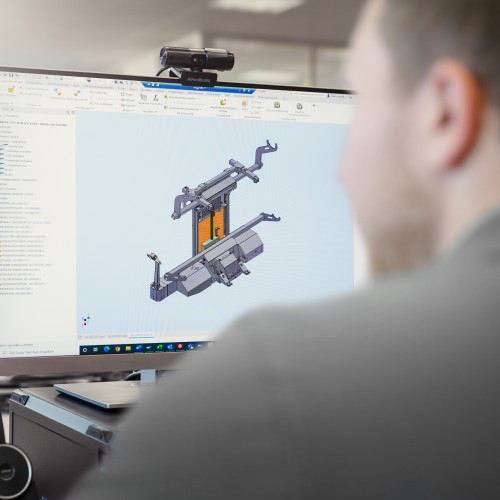
This is where Genkinger comes in:
We will also find a suitable solution for your transport challenge
Standards are the way to go
Move at the first go
more
Rectangular loads such as small load carriers (KLT) or skeleton containers are standardized systems. The fact that they can be stacked on top of each other and/or grouped together next to each other (e.g. on Euro pallets) means that a larger number of the rectangular loads can be transported at the drop of a hat as well as stored in a space-saving manner.
In principle, picking up by forklift or pallet truck is simple. Smaller units are picked up on pallets. Larger boxes, bins or containers have feet that can be driven under from all four sides.
For particularly heavy rectangular loads and uneven distributions, Genkinger will develop special solutions for you for loading, unloading, transporting, storing, as well as feeding within production.
Textile technology for advanced students:
Warp beam change
with weaving harness
For a flexible article change in weaving mills, drawn-in warps must be kept ready on the one hand and picked up, transported and stored in an orderly manner on the other. Warp thread breaks during the changing process and storage must be avoided.
Genkinger has been developing special and standard vehicles as well as devices for the textile industry since 1955. Experienced specialists are needed for individual solutions, especially for warp beam changing including weaving harness.
- Special vehicles and devices for changing drawn-in chains
- For different machine types and widths
- Narrow aisles, full and half warp beams
Project
TLS 20...30: Transport trolley
- Load capacity Q 2000 kg, 3000 kg
- Machine width 600 mm - infinite
Describe your case.
We will be glad to advise you.
Describe your case.
We will be glad to advise you.
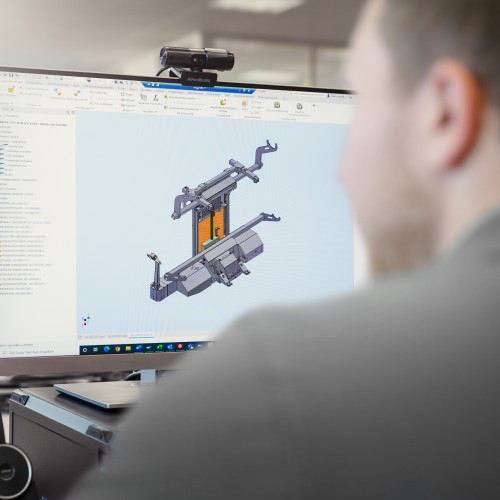
This is where Genkinger comes in:
We will also find a suitable solution for your transport challenge
Our drive:
New mobility
of tools
In order to lift tools safely, transport them and position them precisely in the machine, different load centers, dimensions, docking situations, entry heights and maneuvering options must be taken into account depending on the tool (punch, casting, forging, mold). In addition, there are individual requirements for operation and the degree of automation.
Based on your specification, Genkinger configures mold changers for maximum efficient use on site.
- Handling of tools from 500 kg to over 80,000 kg
- Mobile lifting tables, change carts, assembly aids
- Mobile temporary storage of tools
Things run smoothly with us:
Safe on all
ways through the
weaving and knitting
Special lifting and transport vehicles are needed for inserting, changing and storing warp beams. This is because roll-shaped heavy loads such as warp beams require particularly safe handling.
Genkinger has been the specialist for lifting and transport vehicles for warp beams for many decades. We are in close exchange with leading textile machinery manufacturers to equip small and large textile companies around the world with innovative transport and material handling systems for warp beams.
- Transport and insertion of upper and lower warp beams
- Warp beam change with harness
- For full warp beams, half warp beams, warp beams and canisters
- High lift truck, low lift truck, transport truck
Project
TM/TMD 25: Transport trolley
- Load capacity Q 2.500 kg
- Machine width 300 mm - infinity
Project
KEGU 50: Transport trolley
- Load capacity Q 5.000 kg
- Machine width 600 mm - infinite
Describe your case.
We will be glad to advise you.
Describe your case.
We will be glad to advise you.
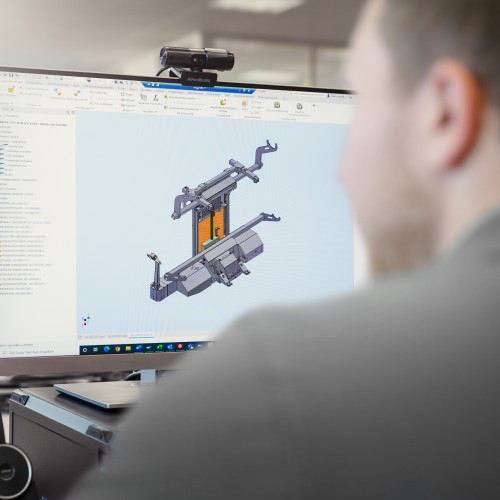
This is where Genkinger comes in:
We will also find a suitable solution for your transport challenge
Highlights
Start project request
Briefly describe your material handling vehicle requirements or tell us about your daily challenges in warehousing technology or textile technology.